Revista Controle & Instrumentação – Edição nº 283 – 2023
|
|
¤
Cover Page
|
|
De robôs a cachorros mecânicos, a automação se populariza em ambientes industriais |
|
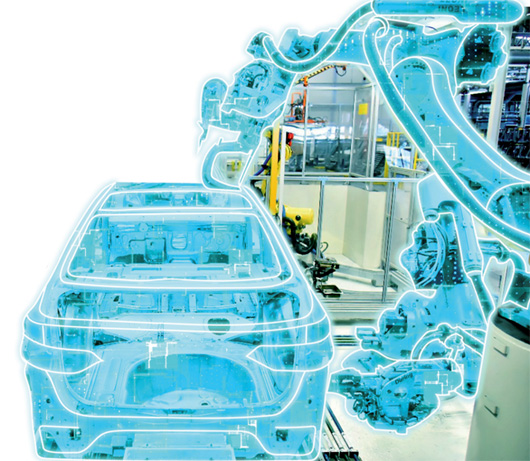 |
|
|
|
|
|
E pisódios marcantes e críticos, a exemplo de mudanças climáticas, Pandemia e guerras, entre outros, de certa forma, estimulam e aceleram o desenvolvimento e a adoção de novas tecnologias, principalmente em atividades repetitivas, ou que gerem algum risco para o ser humano. Os benefícios envolvem, desde a redução do tráfego de pessoas por áreas de risco, a otimização de custos, ganhos em eficiência e produtividade e a ampliação dos níveis de segurança; até o aperfeiçoamento dos profissionais de operação, que passam a tomar decisões em resposta a alertas e a situações não programadas.
Esses desenvolvimentos envolvem integração de robôs e automação móvel, com aplicação de tecnologias controladas remotamente, veículos autônomos, drones, e demais instrumentos e equipamentos, que coletam dados em tempo real, e executam atividades como monitoramento, transporte e movimentação de materiais e inspeção de equipamentos e máquinas, com reflexos positivos nos indicadores de eficiência, flexibilidade e segurança, no ambiente industrial. |
|
Luiz Eduardo Rubião – sócio líder do time de Indústria 4.0 da Deloitte Brasil – cita, entre os expoentes, robôs que “executam tarefas associadas à maior eficiência e à maior segurança da indústria. Podemos ter, por exemplo, drones que fazem a observação de chamas de tochas e a inspeção de vasos de pressão. Mas, não é só isso, podemos hoje pensar em ter uma frota de veículos autônomos e robôs de diferentes tipos, que podem executar suas tarefas e ainda ser acionados para a execução de algumas tarefas emergenciais, em um caso de acidente, por exemplo”. |
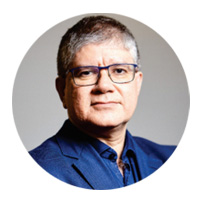 |
|
|
Os veículos autônomos são lembrados por Rubião como alternativa à “utilização de seres humanos em tarefas que podem trazer algum risco para o próprio operador do veículo, ou para terceiros. Também pode reduzir o tráfego de pessoas por áreas de risco”. Listando os drones entre as tecnologias “de grande aceitação no mercado, de impacto significativo e de custo relativamente baixo”, o consultor da Deloitte adiciona o crescente uso de “cachorrinhos mecânicos que fazem a vigilância móvel de sites”.
A difusão dessas tecnologias – e consequente redução dos preços – vem facilitando o acesso às empresas. No entanto, deve ser dada atenção à implantação de um centro de operações integradas desses equipamentos e veículos, com o fim de minorar o que Rubião define como “angústias e frustações” de clientes que, na busca pelo desenvolvimento, fazem investimentos preocupados com o real potencial “de sucesso de cada tecnologia e com a forma pela qual poderão testar e, depois, em caso de sucesso, escalar a aplicação, para que possa ser adotada em diversas outras áreas e sites”, resume.
E ele alerta: “Se as aplicações de robôs e veículos autônomos forem crescendo de forma aleatória ou até um pouco caótica, é difícil imaginar como será a gestão de todos esses itens em uma fábrica. O fato é que, hoje, grandes empresas de automação estão oferecendo sistemas de controles de robôs e veículos autônomos, buscando também usar um protocolo padronizado de comunicação entre os diferentes tipos de equipamentos. No caso de robôs e veículos autônomos, acho que as grandes respostas virão dos primeiros testes a serem feitos”.
A complexidade desses sistemas está diretamente vinculada à inclusão de exceções às regras, dificultando a criação e a implantação. Importante também destacar que a operação desses sistemas exige acompanhamento permanente, devido à possibilidade de comportamentos indevidos, principalmente nas primeiras semanas de implantação, inclusive devido às modificações nos processos |
|
Tradicional usuário de robôs e sistemas de mobilidade em suas plantas industriais, o setor automotivo conta com processos altamente tecnológicos de Indústria 4.0, que envolvem robotização em todas as etapas da produção de um veículo. No caso da Volkswagen do Brasil, como informa Fabrício Valério – gerente executivo de Planejamento de Manufatura da Volkswagen do Brasil e Região América do Sul –, as soluções estão presentes em todas as unidades da empresa neste país. Esses sistemas – para ele – são mais aderentes a processos estáveis e condições controladas.
“A unidade Anchieta, em São Bernardo do Campo/SP, que é a primeira fábrica da Volkswagen fora da Alemanha, por exemplo, é um complexo industrial completo, com centro de pesquisa, planejamento e desenvolvimento de novos produtos, com a mais alta tecnologia e inovação”, explica Valério, frisando que “a mobilidade na indústria é a capacidade de lidar com informações em tempo real, onde quer que estejamos. Quando uma decisão precisa ser tomada, basta acessar uma plataforma e consultar dados, executar tarefas, enviar solicitações, e assim por diante. A assertividade das decisões depende diretamente da qualidade das informações coletadas e de sua disponibilidade, além de protocolos para garantir a integridade do sistema. Na Volkswagen do Brasil, trabalhamos com sistemas de dados altamente tecnológicos, garantindo a troca de informações em tempo real e de forma segura, contribuindo com a produtividade e eficiência do ambiente produtivo”. |
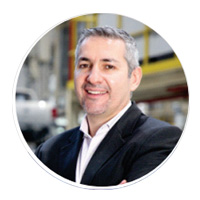 |
|
|
No âmbito industrial, essa integração, para o gerente da Volkswagen, inicia sua jornada nas informações que “deixaram o papel, sendo transferidas para o ambiente digital. Os dados são gerados diretamente dos equipamentos, e interpretados por meio de processos robotizados, utilizando as melhores práticas e protocolos certificados. Esses robôs preparam os relatórios, disparam e-mails e sinalizam os profissionais envolvidos no processo na hora certa, com as informações atualizadas”. |
|
A robotização e a automação industrial são fundamentais para a geração de dados de qualidade em tempo real. Esses dados – afirma Carlos Correa – coordenador de Engenharia de Manufatura da Delphi Aftermarket, marca do conglomerado Phinia – se transformam em informações para tomada de decisão e, como consequência, tornam a empresa em cada vez mais eficiente e competitiva, uma vez que agregam a processos produtivos de alto volume, realizados no chão-de-fábrica, movimentos precisos, repetitivos, com ciclos bem rápidos, inviáveis ao ser humano. |
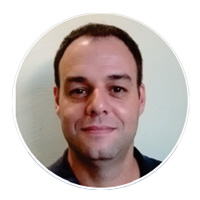 |
|
|
Fornecedora de soluções com especificações de equipamento original, incluindo sistemas de combustível a gasolina, sistemas de combustível diesel, soluções de manutenção, gerenciamento de motores e eletrônica de veículos, apoiados por equipamentos de diagnóstico e teste de nível OE, treinamento e informações técnicas, a Delphi utiliza robôs com auxílio de sistema de visão para detecção das características críticas, dimensionais ou qualitativas, como presença ou ausência de componentes em processos de controle de qualidade, com ganhos de produtividade atingindo ciclos produtivos de 6 segundos, inviável para o ser humano. Outra aplicação robótica usual nessa indústria é a solda laser, pois, “o robô faz o cordão de solda de forma precisa e segura. Atualmente, estamos implementando robôs em processos de montagem para fazer o carregamento e o descarregamento de peças de um processo a outro, de forma precisa e rápida”, informa Correa. |
|
A presença em suas unidades de diversos recursos tecnológicos de automação dos processos que envolvem a produção de seus fertilizantes garante à Yara Brasil mais segurança à operação, celeridade e precisão na produção dos insumos agrícolas. Cesar Augusto Jurinic, gerente de Manutenção do Complexo de Rio Grande/RS, comenta que a unidade de produção da linha YaraVita, localizada em Sumaré/SP, “opera com automatização em quase 100% de todos os processos, sendo que, na unidade misturadora, as máquinas atuam de forma automatizada, na mistura e no envase do produto, com mínima interferência humana”. |
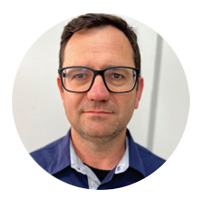 |
|
|
Já o Complexo Industrial da Yara, em Rio Grande – assegura Jurinic – “é o maior e mais moderno parque de produção, mistura e expedição de fertilizantes da América Latina. A automação de muitos processos na unidade trouxe mais agilidade e produtividade, além de melhorar o atendimento ao cliente e o aprimoramento dos controles de qualidade e, acima de tudo, garantiu o desenvolvimento das pessoas, que tiveram a oportunidade de viver programas de qualificação, aperfeiçoando suas habilidades, e fazendo com que o complexo se tornasse referência na indústria 4.0”.
A área mais robotizada da Yara envolve as máquinas de ensaque de fertilizantes em sacos de 50 kg, composta pela integração de três máquinas de fornecedores diferentes, mas que se comunicam entre si através de I/O e rede Ethernet, mantendo a sincronização para garantir um processo contínuo e de qualidade. Elas recebem os fertilizantes a granel e realizam os processos de ensaque, check de peso, paletização, strech e carregamento do caminhão, de forma 100% robotizada, com intervenção humana apenas para abastecimento dos insumos (paletes, bobinas de filmes, bobinas de ensaque).
Outro destaque se reporta ao sistema de ponte-rolante das unidades de mistura, onde há a operação de máquinas complexas, e a automação elimina riscos aos colaboradores, melhora os controles de segurança e qualidade, e otimiza processos. Outro destaque, no complexo gaúcho, é a solução empregada para agilização do recebimento da matéria prima que chega por navio. Trata-se de um píer, onde a carga é descarregada em esteiras instaladas ao longo de 14 km em todo o complexo, e que levam os insumos para as linhas de produção. Jurinic fala, ainda, sobre a existência nessa unidade de um “software logístico, desenvolvido especificamente para nossa necessidade, e utilizado para cadastrar, agendar e monitorar todo o fluxo e o tempo de permanência do caminhão no parque industrial, desde a chegada até a saída com a carga”.
Em Rio Grande, “a integração envolve diversas plataformas, como ERP, DCS e máquinas, e permite, através de CFTV e tags RFID dos caminhões que estão dentro do complexo industrial, o acompanhamento on-line de todos os dados da ordem de carregamento, ponto de carregamento, tipo de produto e cliente, garantindo a rastreabilidade de processos de expedição”, constata o gerente de Manutenção desse complexo industrial.
Um bom projeto de robotização, com periféricos (berços onde o robô irá pegar e colocar peças, esteiras, etc.) bem dimensionados e precisos, agregam produtividade e qualidade ao produto, ampliando a competitividade, certifica Correa, levando ainda em consideração a relação entre qualidade do produto, tipo de processo, e segurança: “Um exemplo de utilização de robôs são processos de solda laser. Os robôs são extremamente precisos, chegando sempre na posição correta determinada, e podem estar expostos a alta temperatura, que para um humano seria demasiada.”
O estudo de viabilidade e o planejamento adequado são essenciais, para que o sistema seja robusto e eficiente. Soluções devem ser viáveis técnica e economicamente. Para isso, é necessário contar com bons profissionais, especificando, integrando e operando o sistema de robotização. E este último ponto é um dos gargalos no processo. |
|
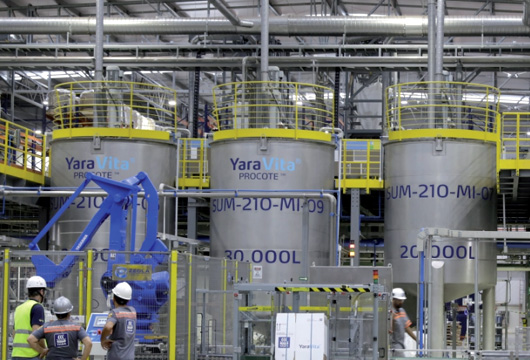 |
|
O caso da Adama comprova a necessidade de um planejamento cuidadoso. Anderson José Tonel – engenheiro de Automação e Controle dessa fabricante de soluções em herbicidas, inseticidas, fungicidas e biossoluções – comenta que os investimentos em robótica e automação se iniciaram há mais de dez anos, envolvendo as áreas de Produção, Processos, Engenharia e TI, sob a liderança da equipe de automação do site. “O ponto de partida foi a visão de futuro, em que se percebeu que a automação seria um grande vetor de diferenciação no mercado. Planos diretores foram elaborados, gerenciados e revisados, ao longo desta última década, sempre com o olhar nas últimas tendências de mercado. Para evoluir, mais importante do que criar e executar as ações de um plano diretor, é estar aberto a possíveis revisões, devido à velocidade das mudanças tecnológicas”. |
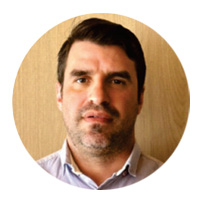 |
|
|
No ICL Group Ltd., a integração também foi paulatina. Como explica Roberto Okuda – engenheiro Elétrico e de Instrumentação dessa indústria química multinacional, que desenvolve, produz e comercializa fertilizantes, metais e outros produtos químicos para fins especiais – “em uma indústria de processo químico, a integração começa com a instalação de um sistema de controle centralizado, que possua recursos para controlar os equipamentos de processo, e enviar dados para o historiador de dados. Em uma indústria voltada para linhas de embalagem, o início é a instalação de máquinas automáticas e robôs. A evolução depende também de ter uma equipe de colaboradores qualificados em automação, e é preciso investir em treinamentos, para preparar o pessoal operacional, técnico e de engenharia”. |
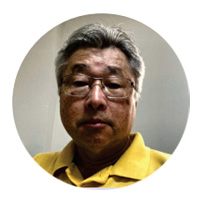 |
|
|
Okuda utiliza a fábrica da ICL em São José dos Campos/SP para materializar sua opinião. Lá, tudo começou em 2000, com a instalação do SDCD Delta-V, para automação das áreas de processo químico das áreas de produção 4, 5 e 8. Em 2010, foi instalado o sistema historiador de dados – PIMS Exaquantum – e, em 2013, ocorreu “a automação das linhas de embalagem, com a instalação de dois robôs para paletização de sacarias. Desde 2020, estamos trabalhando focados na implementação do programa Global de Excelência Operacional, com ações voltadas à capacitação e à melhoria de experiência de nossas pessoas, consequentemente melhorando nossas operações. Todas as iniciativas de automatização de nossas rotinas trouxeram ganhos significativos de capacidade e eficiência, em nossas operações”.
Neste caso específico, o engenheiro Elétrico e de Instrumentação da ICL cita a integração de todos os equipamentos da linha de produção com um desafio, pois, todos devem trabalhar “de maneira uniforme e sem falhas. Se uma máquina da linha de produção não funcionar bem, a linha de produção inteira é prejudicada. A escolha correta do desempenho de cada máquina é importante, porque uma máquina que não produza conforme o esperado vai limitar a produção da linha inteira, mesmo que o robô tenha capacidade para atender à demanda”.
Ao entender a robotização e a mobilidade como caminhos sem volta nas empresas do mundo moderno, se reconhecem as ferramentas da Indústria 4.0, que envolvem robotização, mais eficiência, produtividade e confiabilidade aos processos, como vantagens competitivas importantes para a sustentabilidade do negócio. |
|
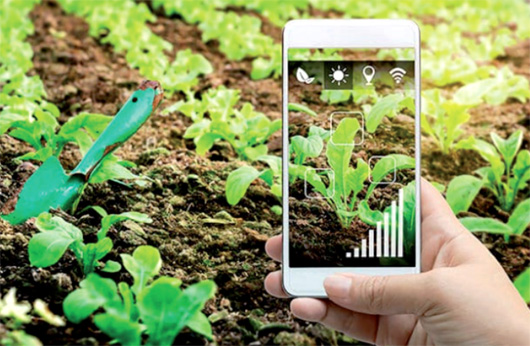 |
|
No caso específico da Volkswagen, como detalhado por Valério, o desenvolvimento da robotização segue duas formas: “uma delas envolve processos corporativos, nos quais a robotização toma uma dimensão interdisciplinar, e exige critérios e protocolos elevados; seu desenvolvimento é restrito e gerenciado por departamentos estratégicos da empresa. A outra forma é relacionada a processos setorizados, nos quais os próprios operadores são estimulados a desenvolver automação, usando ferramentas disponibilizadas pelo grupo. Nos encontros semanais on-line, com participantes de todas as fábricas da Volkswagen no mundo, compartilhamos as melhores práticas”. |
|
<
Fundamentado em sua experiência, Valério elenca a necessidade de aplicação gradativa e de forma assertiva, tanto dos robôs, quanto da digitalização dos dados. O trabalho “com foco na evolução contínua desses processos”, e a convicção na inexistência de uma regra que se aplique a todas as indústrias, são aspectos frisados pelo executivo, assim como a necessidade decorrente do contato com essas tecnologias, que se torna uma prática positiva na empresa, pois, desperta “necessidades e soluções aplicáveis a outros processos”. |
|
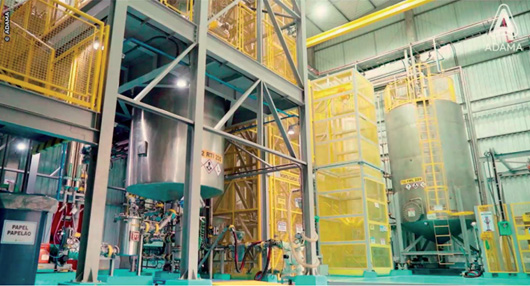 |
|
Nesse contexto, ao envolver as pessoas nesses desenvolvimentos – preconiza Valério – surgem novas demandas, retroalimentando o sistema, o que comprova
que o fundamental é “a forma de atingir a maior quantidade de processos e pessoas, multiplicando as melhorias
provenientes dessa ação”.
Estar aberto à inovação, investir em treinamentos,
capacitar os envolvidos (incluindo operação e mantenedores), é fundamental na visão do engenheiro de Automação e Controle da Adama, do mesmo modo que
implementar um sistema de conectividade que
absorva as necessidades planejadas, pois, a
não adequação da infraestrutura pode inviabilizar a sequência das ações ligadas à robotização e à mobilidade industrial.
A Pandemia e a crise derivada da
guerra entre Rússia e Ucrânia “aceleraram
os processos de digitalização. Em questão
de dias, tivemos de viabilizar as nossas atividades profissionais de forma remota, e permitir que
os dados estivessem disponíveis em plataformas digitais,
acessadas tanto pelos colaboradores que estavam trabalhando presencialmente no processo produtivo, depois
que retomamos a produção, seguindo protocolos rígidos
de saúde e segurança, como pelos que seguiam trabalhando em casa, por conta da Pandemia. Tudo isso, garantindo
a segurança das redes. Dessa forma, a robotização, aliada
à digitalização, trouxe a mobilidade necessária para a indústria enfrentar esses desafios”, admite o gerente executivo de Planejamento de Manufatura da Volkswagen do
Brasil e Região América do Sul.
Também na Adama, a Pandemia estimulou o encontro de soluções que favorecessem o trabalho remoto, e a
continuidade dos projetos e operações, redundando em
investimentos em cibersegurança para monitoramento de
ameaças, controles rigorosos de permissões de acesso,
além de sessões de monitoramento ao vivo, e gravações
para garantir a integridade e segurança das operações.
Além disso, foram estabelecidos mecanismos para o envio seguro de informações das fábricas por meio da web,
garantindo que os dados fossem transmitidos de maneira
protegida e confidencial.
Já para a ICL, a crise sanitária global “mostrou o quão
robusto é o nosso sistema, que permite acessar os dados
de chão-de-fábrica remotamente por qualquer lugar que
possa conectar um computador, e acessar a rede ICL. Os
sistemas automatizados funcionaram perfeitamente, exigindo a mínima presença de pessoal qualificado nas fábricas. A maioria do pessoal pode trabalhar remotamente, mantendo a rotina de fábrica. A fábrica de São
José dos Campos quebrou recordes de produção durante a Pandemia e no início da guerra
entre Rússia e Ucrânia”, confirma Okuda. |
|
Luciano Arantes, gerente de Contas Corporativas da Komatsu, reforça o conceito de atuação remota com a aplicação de caminhões autônomos, assim como trator de esteira e escavadeira teleoperados que levam a mobilidade e a robotização a áreas remotas, de difícil acesso, removendo as pessoas da área de risco, e deixando o ambiente mais seguro, inclusive porque a área central de controle dos caminhões “pode ficar fora do ambiente de mina, seja mina a céu aberto ou subterrânea. Desse modo, se reduzem os gastos de transporte e circulação de pessoas na área de mina, mesmo nas trocas de turnos, que passam a ser realizadas na área onde fica a cabine remota da operação”, minimizando a exposição dos operadores e dos recursos dentro da área de mina, e até favorecendo a reintegração de “funcionários que estavam afastados por alguma limitação na operação convencional”. |
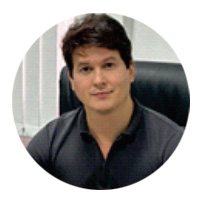 |
|
|
Arantes mostra um novo olhar sobre o processo de robotização e mobilidade de plantas minerárias. Segundo ele, “apesar de os projetos de caminhões autônomos e de teleoperação parecerem ser projetos de tecnologias, na verdade, são projetos de pessoas. Portanto, a gestão de mudança com treinamentos de pessoas é o primeiro passo para a integração da tecnologia na evolução”. Esse também é o principal gargalo alinhado Luciano Arantes, pois a implantação exige adaptação “à mudança, a uma nova forma de trabalho, ao preparo da área para receber a nova tecnologia e entender as limitações. A tecnologia não aceita ‘o jeitinho’. Ou estruturamos o ambiente de aplicação da forma correta, para potencializar o melhor, ou teremos o pior da tecnologia”.
Claro, os resultados devem ser mensuráveis.
Um ponto observado por Tonel envolve o retorno das iniciativas: “Nem todas as vezes é possível obter retorno de investimento de forma imediata (menos do que um ano), dependendo da aplicação específica, da tecnologia utilizada e do ambiente de implantação. Alguns ganhos são imediatos, tais como eficiência operacional, redução de erros operacionais, flexibilidade, segurança, entre outros pontos, assim como diminuição da burocracia e ganhos de agilidade ao negócio”.
Por sua vez, Correa garante que “um bom projeto de robotização deve pagar-se em dois ou três anos, para um projeto de produção em série de cinco a seis anos”.
A variedade de atividades robotizadas na ICL potencializa os ganhos. “Robôs móveis podem transportar câmeras e sensores para inspeção de tanques e equipamentos em locais de difícil acesso. Os Autonomous Guided Vehicle (AVG) transportam paletes e produtos nos armazéns, em outras fábricas da ICL. A mobilidade permite coletar e analisar dados em tempo real, como, por exemplo, variáveis de processo de vazão, temperatura, pressão, etc. A análise da vibração e da temperatura de máquinas permitem à manutenção compreender melhor os processos, e favorece que os equipamentos sejam analisados e estudados com a aplicação de várias técnicas, como análise estatística, análises por softwares usando inteligência artificial, etc.”, enumera Okuda, sinalizando, como ganhos imediatos, o equacionamento de problemas que permite aumento de produção, otimização de processo, redução de perdas, de paradas de produção e de quebras de equipamentos, etc.
O retorno de investimento é diretamente dependente do processo de fabricação. O engenheiro da ICL apresenta um caso ocorrido recentemente, envolvendo a produção de um novo produto, viabilizada pela automação de um reator, com o controle sendo realizado quase que totalmente pelo SDCD. Outro exemplo envolve a instalação de robôs de paletização, que “possibilitou o aumento de produção, de 30 toneladas diárias, para 50 toneladas diárias, porque a parte que limitava bastante a produção era a paletização manual de sacarias de 25 kg. Um outro tipo de robô que tem ganhado bastante atenção, e cuja instalação tem aumentado, é o robô colaborativo (Cobot), que pode trabalhar ao lado do operador, auxiliando-o nas tarefas que exigem levantamento de cargas e inspeção por câmeras”, afirma e reconhece: “O investimento pode ter retorno em menos de cinco anos, dependendo da área”. |
|
Opinião semelhante é a de Carlos Simões, gerente Corporativo de Digitalização Industrial da M. Dias Branco. Ele relaciona o payback ideal para o investimento em mobilidade robótica a vários fatores, como o custo inicial, os benefícios esperados e a indústria. Normalmente, espera-se que ocorra em um período que varia de um a cinco anos, mas isso pode ser mais curto ou mais longo, dependendo das circunstâncias. |
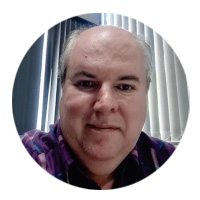 |
|
|
“Os motivos envolvem, entre outros fatores, o custo inicial elevado: o investimento inicial na aquisição de robôs móveis, sensores e tecnologia associada pode ser significativo, o que pode ser um obstáculo para algumas empresas, especialmente as de menor porte; integração complexa de sistemas de mobilidade robótica com infraestrutura existente, como sistemas de automação industrial e sistemas de gerenciamento, pode ser complexa, e requer expertise em engenharia; conformidade regulatória, uma vez que, em muitos setores industriais, existem regulamentações rigorosas que precisam ser seguidas, e a implementação de robôs móveis, podem exigir conformidade com essas regulamentações; e escalabilidade, pois, à medida que a operação cresce, a escalabilidade dos sistemas de mobilidade robótica pode ser um desafio, uma vez que pode exigir aquisição de mais robôs e infraestrutura adicional”, anuncia Simões. |
|
Ganhos imediatos computados pela Yara Brasil, principalmente no complexo Rio Grande, compreendem aumento de produtividade, como consequência do automatismo e do monitoramento dos caminhões; ganhos em segurança e diminuição de risco de furtos de carga, por conta de sistemas de biometria, OCRs e controles de acessos limitados apenas ao produto determinado para carregamento; redução de erros humanos, e melhor alinhamento e produtividade entre as equipes. |
|
A redução do tempo de espera do caminhoneiro na fila é definida por Jurinic como “bastante impactante, colaborando assim com nosso comprometimento nos prazos de entrega e satisfação do cliente”, que recomenda a cada indústria discriminar “os gargalos de sua unidade produtiva, e entender quais procedimentos podem ser automatizados para iniciar esta integração e evoluir nos processos”. Soma, ainda, parâmetros de qualidade da carga, e a facilidade na descarga do produto na lavoura, pois, já chega paletizada ao cliente. |
|
“Acreditamos que a automação só acontece e prospera porque há por trás de cada processo uma equipe competente e qualificada para que cada etapa seja concluída com excelência, e temos a transferência de conhecimento um legado humano muito presente na companhia”, detalha Jurinic. |
|
|
LEIA MAIS
NA EDIÇÃO IMPRESSA |
|
DESEJANDO
MAIS INFORMAÇÕES: redacao@editoravalete.com.br
|
|
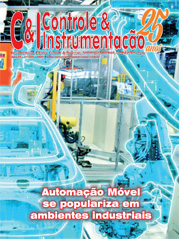 |
Clique na capa da revista para
ler a edição na íntegra |
|
|