Revista Controle & Instrumentação – Edição nº 276 – 2022
|
|
¤
Cover Page
|
|
Setor de petróleo e gás vence desafios da digitalização com pesquisa e dados |
|
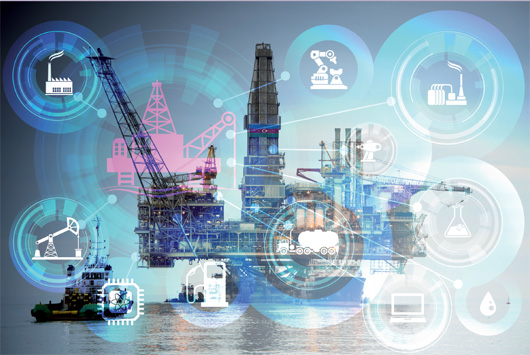
|
|
|
|
|
|
Há algum tempo, os líderes da indústria de petróleo
e gás global previam que o setor evoluiria
com maior diversificação e uso de tecnologias
para inovar – com consequente aumento do risco
cibernético. E, como aponta um estudo da BDO Global
para a indústria de petróleo e gás, a inovação pode ser
uma tábua de salvação – usada para otimizar finanças
e operações – ou um calcanhar de Aquiles – ignorado,
até que seja tarde demais. Seus analistas apostam que,
a inovação, aliada à evolução das prioridades do setor
de petróleo e gás, mudará o cenário, com aplicação de
nanotecnologia – mas não só ela – em todas as fases do
ciclo de vida – da exploração e perfuração de avaliação e
produção, transporte e refino. De fato, os analistas veem
o mercado digital em petróleo e gás ultrapassando os US$
20 bilhões, com aumento substancial em segurança cibernética,
e esperam mudanças na tributação dos derivados
de petróleo, como meio de controlar a demanda e atender
metas ambientais.
As apostas tecnológicas não ficam no setor produtivo:
espera-se que quase metade de todos os contratos
do setor usem tecnologia blockchain para mais rapidez,
precisão e menos espaço para disputas – resposta à busca
por soluções digitais para os desafios enfrentados nas indústrias
de óleo e gás.
Nesse cenário, algumas tendências se destacam na
produção, as mais voltadas para a otimização dos processos
de manutenção e transição energética, como análise
de equipamentos críticos/análise preditiva de falhas; manutenção
preditiva e descarbonização. Porque a produção
de petróleo e gás deve ser segura, disponível e ter
uma pegada de baixo carbono. Mas, o custo de capital das instalações precisa cair, e isso pode ser feito introduzindo
conceitos-padrão e modulares de fabricação inteligente.
Estandardização e interoperabilidade de dados,
no projeto e nas operações, também podem reduzir os
custos de investimento e operação.
Entram aí os conceitos da Indústria 4.0, que oferecem
novas formas de trabalhar em petróleo e gás. Eles
fornecem uma maneira de introduzir a engenharia digital
de ponta a ponta, para toda a vida útil de uma instalação.
Dentro dos conceitos da Indústria 4.0, cadeias de valor
integradas podem ser construídas, diminuindo custos de
engenharia, aquisição, construção, modificações e manutenção
de projetos; cadeias de valor integradas abertas
para novos modelos de negócios e colaboração na indústria
– com base em dados e serviços baseados em dados.
A padronização que chega junto com esses conceitos
permite instalações sob medida com plantas mais simples
e robustas, e um grande potencial para introduzir
robótica e autonomia nas operações.
Mais importante ainda, a Indústria 4.0
fornece uma integração vertical eficaz das
instalações da indústria de petróleo. Isso torna
mais simples a obtenção de dados para o
tomador de decisão.
As instalações que implementam os
conceitos da Indústria 4.0 perceberão os objetivos
do campo do futuro, e isso está sendo
facilitado com tecnologias como Redes sem
fio, 4G e 5G; instrumentos com sensores
independentes para processos e monitoramento,
geralmente não invasivos e fáceis de
instalar; equipamentos inteligentes; adoção
acelerada da Internet Industrial das Coisas (IIoT), que oferece
formas alternativas de integração de instrumentação,
equipamentos e sistemas de controle; uso de protocolos
padrão e plataforma aberta OPC-UA; automação aberta
e computação em nuvem.
A diferença é que a Indústria 4.0 propõe uma mudança
para uma rede em vez de uma hierarquia, e a IIoT
é uma manifestação dessa abordagem de pensamento em
rede. A Indústria 4.0 se baseia em automação e controle,
tendo como padrões a ISA95 e OPC; a base da IIoT
está na ciência de dados, computação e eletrônicos. São
perspectivas complementares e necessárias que precisam
trabalhar juntas, à medida que TO/TA e TI interagem.
E a implementação da Indústria 4.0 no setor de
petróleo e gás envolve a construção dos Digital Twins
– gêmeos digitais – para otimizar projetos e operações.
E, como outros setores, o de petróleo e gás também enfrenta
o desafio de implantar os gêmeos digitais no seu
parque já instalado, com o agravante dos descomissionamentos,
que envolvem centenas de vertentes e todas com
interfaces ambientais. É importante frisar que a Indústria
4.0 não é sobre descontinuação do que existe, mas sobre
melhorar o que se faz, automatizar os processos e aproveitar as oportunidades das novas tecnologias, encontrando
maneiras eficientes de trazer esses campos para
o ecossistema digital, sem desperdiçar dinheiro em ativos
que podem ser desativados. De fato, o descomissionamento
pode fornecer um incentivo para a digitalização
das informações do projeto.
Essa transformação digital que avança no setor de
petróleo e gás envolve reconhecer a enorme quantidade
de dados que são gerados nos processos, a grande oportunidade
que as novas tecnologias proporcionam para
transformar a forma de operar o negócio, como descobrir
meios para continuar trabalhando em um mundo que
está por vir – e ao mesmo tempo já está aí.
É muito interessante observar que essa transformação
digital e a aplicação das tecnologias envolvidas não é
apenas para grandes estruturas. Pode ser aplicada a sistemas
isolados, ou mesmo equipamentos. |
|
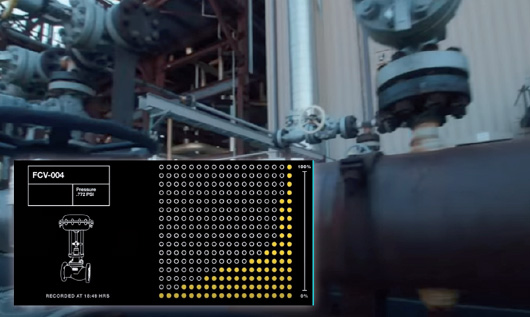 |
|
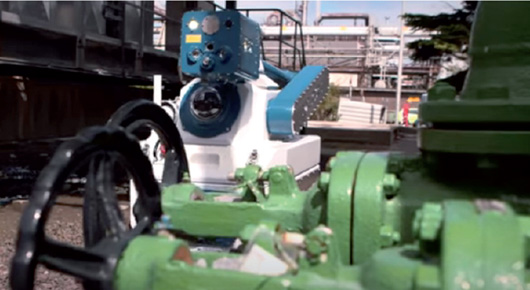 |
|
Vale ser observado o que uma grande companhia
de petróleo fez a partir de uma válvula de controle
que falhou e fez o processo oscilar, e acabou por quebrar
o corpo da válvula – o que custou algum tempo
de parada não planejada. Pensando em como usar os
dados já coletados para evitar falhas futuras, o departamento
de ciência de dados da companhia usou
os dados para elaborar modelos de aprendizado de
máquina, orientados para detectar anomalias que não
seriam percebidas de outra forma. E o que começou
com uma válvula se tornou um teste em outras 15,
e depois para milhares de válvulas. Mas, essa é uma companhia global; como dimensionar e executar isso
globalmente? A companhia não fez uso de historiadores
de prateleira, e não tendo a pretensão de ser
uma empresa de IA, chamou uma empresa de desenvolvimento
de modelagem de manutenção preditiva,
com quem já trabalhavam em outras frentes. Juntas,
as equipes desenvolveram algoritmos, para identificar
falhas de concepção com níveis muito altos de precisão,
através da tecnologia Predictive Analytics, uma
extensão da Inteligência Artificial.
O desafio era dimensionar e implantar a solução em
seus algoritmos de aprendizado de máquina para toda
companhia porque, ainda que a mecânica da válvula seja
simples, o contexto interfere, o que significa que é preciso
pelo menos um modelo independente de aprendizado
de máquina por válvula. E, ao final, a plataforma da empresa
contratada foi capaz de gerenciar 2 milhões desses
modelos.
Então, as equipes desenvolveram juntas mecanismos
para monitorar mais de 8.000 equipamentos, todos os
dias, incluindo dados coletados por robôs, que podem
monitorar a posição das válvulas manuais, podem detectar
vazamentos, vazamentos de gás, vazamentos de líquidos.
E com esse trabalho diário, a companhia de petróleo
pode responder de maneira mais rápida e responsável.
Como nem toda empresa tem uma equipe de cientistas
de dados, para muitos casos, os sistemas comerciais
têm ferramentas que encaminham bem esses problemas
– talvez não para dois milhões de modelos, mas com certeza
para algumas centenas. E tem muita gente envolvida
em melhorar esses processos, e aumentar as capacidades,
de maneira segura.
Se quisermos ser realmente bem-sucedidos numa
transformação, temos de trabalhar com um ecossistema
mais amplo de parceiros, onde todos se beneficiem.
Nessa linha, aconteceu uma chamada pública conjunta
entre Finep – financiadora de estudos e projetos – e o
conselho norueguês de pesquisa (RCN), cofinanciados
por empresas no Brasil que compõem o Consórcio Libra,
entre elas a Petrobras, e, na Noruega, pelas empresas
Shell e Equinor. Esta chamada pública foca na completa
digitalização do processo produtivo em gêmeos digitais
(Digital Twins), que permitem acompanhar e otimizar
todas as condições de produção de uma planta de petróleo.
O Grupo de Pesquisa Sistemas de Computação
para E&P de Petróleo do INF-UFRGS, e o Sirius Lab da
Universidade de Oslo (UiO), ficaram responsáveis por
esse projeto inovador.
“Nosso objetivo no Projeto Petwin de gêmeos digais
para otimização e gerenciamento da produção de petróleo
e gás é otimizar e gerenciar a produção; é um projeto
de pesquisa que envolve vários parceiros, cada uma das
partes contribuindo nas suas competências. A ideia é fomentar
a cooperação internacional para esta área de digital
twins, e ter um resultado prático que possa ser aplicado pelas empresas”, conta o professor Dr. João Cesar Netto,
do INF – Instituto de Informática da UFGRS – Universidade
Federal do Rio Grande do Sul.
Mas, não apenas pelas empresas participantes, para
toda a comunidade, incluindo as provas de conceito
– obviamente os dados secretos/sensíveis das empresas
participantes não serão publicados –, os resultados práticos
de ferramentas, relatórios, conclusões e artigos. Nem
poderia ser diferente, já que é uma chamada pública para
promover a inovação – que virá através de aplicações
dessas pesquisas do grupo.
“A gente faz a pesquisa e deixa os resultados num
nível de maturidade que prova o conceito demonstrado
num ambiente relevante, ou seja, provamos que ele
funciona. E aí o desenvolvimento na forma de produto
acontece pelo mercado. Estamos na fase em que há a demonstração
de conceitos e funcionamento de protótipo
em ambiente relevante, porque trabalhamos com dados
reais para demonstrar que é possível. Posteriormente,
uma empresa pode desenvolver um produto comercial
baseada nesses conhecimentos. A função da universidade
é justamente permitir que todos tenham acesso a possibilidades
de levar inovação para as diversas empresas
e setores.” |
|
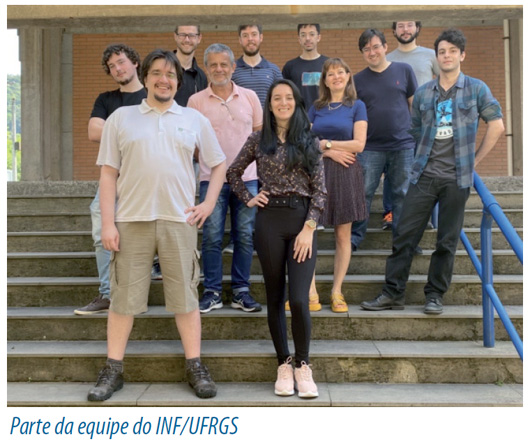 |
|
Um gêmeo digital é uma representação virtual de
um sistema real físico, com os dados desse sistema físico
monitorados em tempo real – ou tempo de operação
–, ou seja, se acontece um evento no local físico, ele é
imediatamente transmitido para o modelo representado,
dando acesso a todos os dados que estão acontecendo
no mundo físico. É uma representação digital dos
equipamentos reais, e daquilo que acontece neles com
todos os dados durante a operação, ao longo do tempo.
Se muda a temperatura num determinado ponto, isso é
registrado no local físico, e também no gêmeo digital,
para que se possa trabalhar com eles de forma simultânea
com a operação.
O gêmeo digital é um
grande concentrador dos
dados do que está acontecendo
no mundo físico.
Ao mesmo tempo que se
monitora, se podem tomar
ações preventivas,
como por exemplo um
ponto da cadeia de escoamento
está com pressão
alterada e, com uma
ação preventiva, se pode
melhorar a condição de
operação do sistema. Ou,
a verificação de integridade,
como por exemplo,
quando a temperatura de
terminado equipamento não pode passar de determinada
medida, porque isso pode gerar danos sérios – com o
gêmeo digital se pode intervir automaticamente.
“Entrando no mundo do Data Science, também posso
usar os dados do que já aconteceu, e fazer previsões
do que vai acontecer, e o que pode ajudar a sustentar
ou aumentar a produção em determinado momento, depois
de tomar ações recomendadas para a otimização do
processo. Com esse volume de dados, se pode simular “o
que aconteceria se” – e as possibilidades acompanham a
imaginação, como o que aconteceria se um equipamento
injetasse 10 unidades de gás, ao invés de O2? O que aconteceria
com a integridade e com a produção? Posso ter
aplicações que usam esses modelos computacionais para
fazer previsões de cenários, sem ter de experimentar isso
no mundo físico – essa é uma das grandes vantagens dos
gêmeos digitais. E ainda, usando a massa de dados que fui
coletando ao longo de tempo, eu posso aplicar as novas
tecnologias de inteligência artificial e machine learning ou Aprendizado de Máquina, para prever comportamento,
verificar se existem anomalias, e outras aplicações. Note
que, para boa parte das aplicações baseadas em Inteligência
Artificial e Aprendizado de Máquina, é preciso ter
conteúdo, é preciso ter dados. E o gêmeo digital permite
ter esses dados integrados num lugar único – porque tenho
como acessá-los de um ponto único – sejam dados
do sistema de automação, de manutenção ou das diversas
suítes do SAP. E com essa disponibilidade, se pode fazer o
planejamento da produção, e colocar algoritmos inovadores
de aprendizado de máquina para fazer previsões em
diversos pontos das plantas”, conta o Professor Netto. |
|
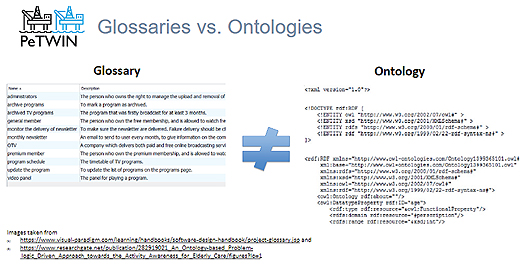 |
|
Existem desafios que o projeto procura resolver,
como a unificação da nomenclatura ou a compatibilização
dos significados e nomenclatura desses dados. Porque
um engenheiro de automação pode denominar um
objeto de maneira diferente do pessoal de gestão; cada
área tem um jargão, e o desafio é ter uma visão compatibilizada
desses dados, ou seja, quando se fala de uma temperatura de um elemento, todos os acessos ao banco
de dados vão referir-se de uma forma única àquele objeto
e valor associado.
Então, essa unificação utiliza inglês? Sim e não.
O Professor Netto explica que, quando se desenvolve
uma ontologia (vocabulário+significado), também se
agrupam vários sinônimos, e se orienta a utilização dos
dados com base no seu significado.
No PetTwin o foco é demonstrar aplicações que
possam dar insights de melhorias e otimização – como
um determinado poço vai desenvolver sua produção,
por quantos anos, e a partir de qual época é preciso
agir para otimizá-lo, e de que maneira. Mas, o projeto
não é restrito a isso. Pode ser aplicado à manutenção,
e o grupo de pesquisadores já está desenvolvendo uma
aplicação, valendo-se do fato de que, para gerar aprendizado,
é preciso volume de dados. Mas, como trabalhar
com equipamentos com uma falha rara, uma taxa de
falha pequena? |
|
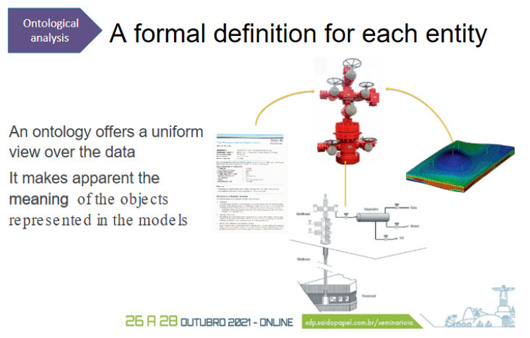 |
|
“Há dificuldade de aplicar algoritmos de aprendizado
de máquina, quando não existe um histórico de
base, mas, com o Gêmeo Digital, se pode simular comportamento
de falhas e, a partir daí, ter massa de dados
para rodar o algoritmo de IA, e fazer predição de falhas
em equipamentos que têm baixo índice de falhas, mas
alto risco. Por exemplo, pode-se aplicar no Gêmeo Digital
de uma válvula subsea, que dura muitos anos sem
uma falha sequer, mas que, se falhar, pode gerar derramamento
de óleo. Então, através do Gêmeo Digital,
se pode modelar o tempo, passando mais rápido que o
real, fazendo com que as falhas apareçam no ambiente
virtual, coletando esses dados, e colocando para rodar
o algoritmo, e aí, então, fazer a predição para a válvula
do mundo físico, a válvula real”, resume o professor
Netto.
Assim, de maneira segura, se consegue gerar um
conjunto de dados, que modelam um grande espaço de
tempo, equivalente ao que ocorreria na realidade. Mas,
os Gêmeos Digitais se sobrepõem aos já existentes gerenciadores
de ativos comerciais?
“Não. Os gerenciadores fazem bem seu trabalho,
mas suas bibliotecas estão separadas, às vezes isoladas,
ou têm utilização apenas no seu próprio espectro
de aplicação. A ideia do Gêmeo Digital é que o historiador
que existe nesse sistema comercial seja uma
de suas fontes de dados; um CLP seja outra fonte de
dados; o sistema de manutenção outra fonte; tudo o
que o pessoal fez durante o tempo de projeto, outra
fonte. E o Gêmeo Digital busca reunir e prover acesso
inequívoco para as aplicações. Então, sempre que
se buscar a temperatura de um equipamento, através
da unificação e da organização dos dados, independentemente
do nome que ele tenha no historiador ou
no ERP, o Gêmeo Digital vai saber exatamente o que
está usando. Sua interface única proporciona a visão
integral de todo o fluxo dos processos – causas e efeitos
estão integrados, e são visíveis no Gêmeo Digital”,
destaca o professor Netto.
O PetWin está rodando há 18 meses, mas ainda
leva algum tempo para terminar. As interações entre os
diversos pesquisadores acontecem em reuniões periódicas.
Para o desenvolvimento das provas de conceito,
protótipos e estudos de caso, a equipe recebe situações
verdadeiras, e trabalha com dados reais, porque a ideia
é de que, no final dos 42 meses, se tenham definições
pertinentes da integração dos dados, que esteja pronta a principal parte da ontologia relativa à produção, e protótipos
que demonstrem a viabilidade de como desenvolver
soluções a partir dele. |
|
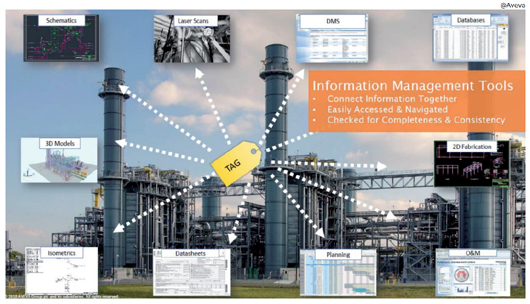 |
|
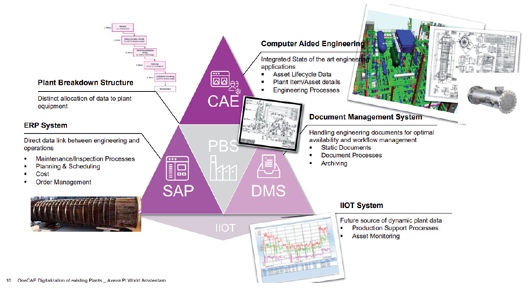 |
|
O grupo de pesquisadores já tem resultados bem
interessantes da conceituação e aplicação do Gêmeo
Digital. É bem aguardado o desenvolvimento de como
fazer um Gêmeo Digital de uma planta brownfield
– que vem sendo elaborado através das empresas parceiras
e do professor especialista em modelagem.
Uma empresa que já iniciou o caminho para o
desenvolvimento de um modelo de dados para seus
ativos (equipamentos, instrumentação e pipelines) e
operações é a Evonik. Esses modelos permitem um
cenário independente do fornecedor de ferramentas
de software. Um aspecto do modelo de dados dos ativos
é que ele associa uma sequência de nomenclatura
exclusiva, por exemplo, uma estrutura de quebra de
planta, a um ativo específico. Uma planta inteira pode
então ser mapeada e preenchida com atributos definidos
pelo modelo de dados. De fato, outras fontes de
dados, como sistemas de gerenciamento de documentos
e modelos 3D, também podem ser vinculadas. Isso
fornece dados contextualizados para os usuários, que é
o valor que se busca nesses projetos.
O modelo de dados é a tecnologia central para um
Gêmeo Digital, e um grande desafio para realmente utilizar
a tecnologia é a cultura e as pessoas necessárias para
modernizar a maneira de trabalhar.
A Evonik reconheceu o desafio adicional de implementar
o Digital Twin em uma fábrica que já está em operação
e um esforço conjunto está em andamento para
criar roteiros específicos das plantas para a implementação
de tecnologias digitais – o que vai levar tempo e consumir
recursos significativos para implementar a mudança,
mas a empresa está certa de que o desenvolvimento
agregara valor ao negócio.
As equipes que estão trabalhando com o Gêmeo
Digital na Evonik esperam realizar economias em várias
frentes: na eficiência de engenharia para projetos
de capital, o que é especialmente verdadeiro para otimizações
de plantas existentes; na troca de dados com
parceiros externos com base em padrões internacionais;
na entrega de dados para produção no final de um projeto;
no planejamento de manutenção mais rápido, com
instruções passo a passo virtuais com os fornecedores;
e outras.
O Professor Netto lembra que a necessidade de
um especialista para fazer uso de produtos de prateleira,
e mesmo de resultados de pesquisas, depende
do momento em que se vai utilizar a solução, porque
o Gêmeo Digital é aplicado a todo o ciclo de vida de
um processo.
O que o mercado pode ter certeza hoje é de que
o Brasil tem gente capacitada para atendê-lo. O INF/
UFGRS tem uma equipe com 8 bolsistas BCIT de graduação;
6 mestrandos propondo novos algoritmos; 5
doutorandos trabalhando na fronteira do conhecimento
de arquitetura e modelo de dados, além de ontologia;
3 pós doutores, que já trabalharam na indústria
em diversas áreas; 2 mestres para suporte. A equipe
grande e multidisciplinar tem ainda 8 professores e
muitos alunos da graduação, inseridos nos temas afetos
ao projeto, que se tornam aptos para atuar nas áreas
relacionadas. |
|
<
|
|
|
|
|
|
|
|
LEIA MAIS
NA EDIÇÃO IMPRESSA |
|
DESEJANDO
MAIS INFORMAÇÕES: redacao@editoravalete.com.br
|
|
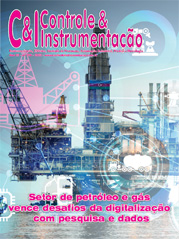 |
Clique na capa da revista para
ler a edição na íntegra |
|
|