Revista Controle & Instrumentação Edição nº 143 2008
|
|
¤
Cover Page
|
Conectando... |
De olho no potencial da linha de produção, empresas integram sistemas de gestão corporativo com controle do processo |
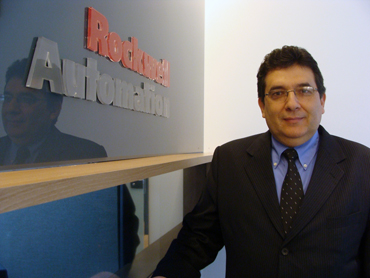 |
Egreja: oportunidades de ganho encontram-se na linha de produção
|
|
Depois de mais de uma década investindo maciçamente nos sistemas de informação no nível corporativo, as empresas se deram conta de que as possibilidades de ganho já começam a rarear. E também que as oportunidades mais claras agora se encontram na linha de produção. Não são poucas as indústrias que já contabilizam os benefícios de colocar um dado de produção para trabalhar de forma colaborativa com os sistemas corporativos.
Um levantamento feito pela Rockwell Automation a partir dos índices de rendimento, funcionalidade e performance demonstrados por uma centena de indústrias de vários segmentos, apontou um abismo entre quem já adotou a integração de seus sistemas e as empresas que ainda não trilharam esse caminho – um número que impressiona quem teve acesso a pesquisa é a lucratividade quatro vezes maior das empresas que já tinham sistemas integrados.
E esse é o principal motivo destacado pelo gerente regional de software da Rockwell Automation, Luiz Roberto Egreja: em um mundo altamente competitivo, nenhuma empresa, por melhor que seja, não pode se dar ao luxo de ter um concorrente quatro vezes mais lucrativo. “Algumas empresas já perceberam esses ganhos e estão investindo – tanto que as tendências de investimento no mercado estão apontando nessa direção. Mas existem outras empresas que, por ainda não terem passado pela experiência, ou não ter bem definidos os processos de avaliação do retorno sobre esses investimentos, não conseguem enxergar esse beneficio”.
Essa questão de integração entre os sistemas corporativos ganhou impulso na Rockwell Automation após o acordo feito com a Cisco Systems – que aportou expertise em tecnologia de redes às suas plataformas de controle de processos. Nos vários eventos que as duas empresas já promoveram para apresentar as possibilidades da convergência, as questões levantadas pelos gestores de plantas mostram que as empresas já se convenceram das oportunidades de ganhos possibilitados pela integração dos sistemas – só que nem sempre conseguem traçar uma estratégia que realmente preencha os gaps e traga todas as possibilidades de ganhos. E, sem dimensionar o retorno de maneira clara, o projeto dificilmente passa pelo crivo do board que vai tomar a decisão de investimentos da empresa.
Analisar essa integração, no entanto, não é um trabalho fácil. Sob o enfoque tecnológico, a convergência entre a tecnologia de informação e a automação dos processos está praticamente resolvida – basicamente se resume a interligar a instrumentação do processo a um switch Ethernet/IP e transferir seus dados em CIP (Common Industrial Protocol) para qualquer terminal da rede.
Claro que ainda existem várias questões a serem definidas – a segurança é a maior delas. Mas os benefícios não surgirão simplesmente pela adoção da tecnologia – e sim pela combinação da tecnologia com a capacitação dos profissionais, o processo e os modelos de gestão adequados para tirar o melhor proveito de todo o investimento. “Não adianta fazer um fantástico projeto de rede, colocar os melhores sensores, conectar todos os equipamentos, e esperar que a lucratividade aumente quatro vezes. Os melhores casos de sucesso são aqueles onde esses componentes trabalharam de forma coordenada”, ressalta Egreja.
Um exemplo claro disso são as empresas que, mesmo depois de integrar os sistemas e coletar os dados on-line, continuam avaliando seus indicadores de performance em uma reunião semanal – da mesma forma como faziam quando os dados eram coletados em papel e tabulados em uma planilha em Excel. A integração permite que os operadores – e também os gerentes de planta – acompanhem os dados em tempo real – e cada um trabalhe essa informação sob sua perspectiva. |
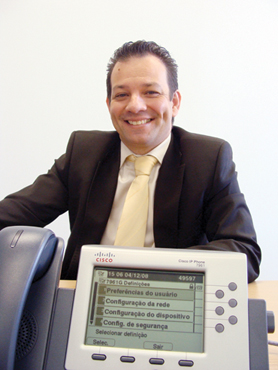 |
Amri: benefícios começam a ser percebidos quando a vários serviços são utilizados na rede |
|
Boas práticas...
A questão mais apontada por quem ouve falar em integração é a vulnerabilidade do sistema. Na prática, a integração dos sistemas deve vir acompanhada de tecnologias e práticas de proteção – que até então não eram tão fundamentais no chão de fábrica. A probabilidade de um ataque externo – seja de um hacker ou de um vírus – ao sistema de controle é proporcional à abrangência da rede: quanto mais sensores estiverem conectados a uma rede Ethernet que transporte dados até o ERP ou à web, mais exposto estará o controle da planta. Assim, o benefício tem que ser maior do que os riscos – se o projeto não prevê uma forma para mitigar esses riscos, a empresa pode perder todos os ganhos de produtividade no primeiro ataque de um vírus.
A recomendação é que o projeto seja desenhado em cima de normas – a principal para integração do ambiente corporativo com o chão-de-fábrica é a ISA S-95, que define fluxos de dados, funcionalidades, interfaces. A S-95 divide o sistema em diferentes níveis – instrumentação, controladores, sistemas de operação, sistemas de gestão de operação, MES, ERP e até o BI.
“Essa norma garante que os projetos de integração sejam feitos em menores prazos, com menor risco e menores custos – e que quando for necessário trocar o MES ou o ERP, a nova versão vai seguir o mesmo padrão”, explica Egreja, lembrando que os primeiros projetos demoravam 18 meses para serem implementados – e hoje não levam mais de dois meses.
O pecado da S-95 é não abordar a questão da segurança da informação – e por isso é necessário recorrer à norma S-99 para garantir que essa troca de informação entre os vários sistemas permaneça inviolável.
A Rockwell e a Cisco criaram um guia de referência – chamado Arquitetura de Referência – que define boas práticas para implementar um projeto IP baseado na norma S-95 atendendo a todos os requisitos de segurança da S-99 e usando as tecnologias e os produtos disponíveis no mercado.
Normas e boas práticas são fundamentais nesses casos – em que existe uma área de intersecção entre a automação e a tecnologia da informação, onde os experts ainda não transitam com confiança. Mas outro viés importante é a instrumentação – alguns já disponíveis, como o switch Stratix 8000, produzido pela Rockwell Automation com a tecnologia Cisco – para implementar uma arquitetura que atenda todos os requisitos de segurança, de disponibilidade, e que resista ao ambiente industrial – e que precisam incorporar ferramentas de configuração familiar aos engenheiros de automação industrial e de TI. “É importante observar que um switch industrial, por si só, não garante a performance, a disponibilidade e a confiabilidade que um ambiente de automação requer. O que faz a diferença é a forma como eles são arranjados, por isso a importância da arquitetura”, destaca o gerente da Cisco Systems para o segmento automotivo, Amri Oliveira.
A maioria das aplicações ainda está em desenvolvimento nos laboratórios – como os controladores com microswitches integrados. O Power over Ethernet – PoE é um exemplo claro: a tecnologia permite que instrumentos sejam energizados pelo próprio cabo de rede. Existem alguns desafios – como o uso em áreas classificadas – mas o caminho da migração está desenhado. O segredo é ter uma arquitetura que seguirá em evolução, sem jogar fora o que já existe.
“Substituir a rede de instrumentação levará um tempo, e talvez a principal prioridade nesse momento seja a integração entre sites, algo que reforça a idéia de arquitetura e prevê o uso de switches e roteadores convencionais”, complementa Amri. |
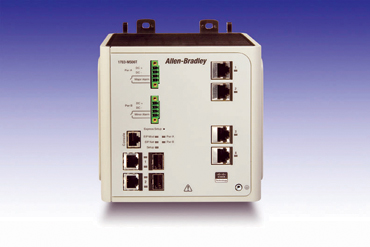 |
Stratix 8000: switch permite construir redes de comunicação para conectar inversores, controladores, computadores e interfaces homem-máquina |
|
Além da rede de campo...
Amri ressalta que os benefícios da Ethernet industrial – uma rede com switches mais sofisticados do que os convencionais – só começam a ser realmente percebidos quando a empresa passa a usá-la como uma rede multiserviços, com aplicações que vão além do trafego de dados. “Quem fizer um projeto de rede Ethernet pensando apenas na substituição do fieldbus, terá apenas mais uma rede entre as várias que estão no chão-de-fábrica. Quando falamos em arquitetura, é como se criássemos uma infra-estrutura unificada, que vai suportar as redes de campo, as aplicações de vídeo que demandam alta largura de banda, redes sem fio, e aplicações que necessitam de qualidade de serviço, alta taxa
de transmissão ou são sensíveis a atrasos”.
Já há um consenso entre os engenheiros sobre o futuro das redes: que o Ethernet irá se tornar a rede utilizada por toda a empresa – e que o Ethernet/IP será a espinha-dorsal dessa integração entre as várias células do chão-de-fábrica e outros níveis e plantas da corporação. Mas até que isso se torne uma realidade presente no ambiente industrial, barramentos de várias denominações continuarão transportando dados entre os instrumentos e os sistemas de controle. “Ninguém irá jogar fora todos os equipamentos, redes e sistemas legados que têm hoje – até porque é mais difícil justificar economicamente a substituiçào de algo que foi instalado há poucos anos e que está funcionando sem problemas”, lembra Egreja.
Esse Ethernet/IP utiliza os seis primeiros níveis da camada de protocolo OSI – que são idênticas em todos os protocolos de rede. Muda apenas o protocolo de aplicação CIP, que pode rodar em cima de um meio físico Ethernet, Devicenet, Controlnet ou qualquer rede padronizada pela ODVA.
Se há um consenso entre toda a comunidade envolvida é que esse trabalho de integração não será realizado apenas pelos engenheiros de automação nem pelos especialistas em TI – muito menos será resolvida exclusivamente pelos fornecedores de instrumentação ou de sistemas de controle. A resposta nascerá a quatro, seis ou oito mãos. |
A pergunta certa |
|
A Companhia Cacique de Café Solúvel foi fundada em Londrina/PR, em outubro de 1959, por Horácio Sabino Coimbra que, com privilegiada visão de negócios, começou a exportar, já em 1965, café solúvel tipo spray dried para a Rússia. Ainda hoje a região da antiga União Soviética é um dos maiores mercados da empresa. Em 1968, fabricando o solúvel granulado, a empresa duplica a capacidade de produção e, na década de 70, a Cacique assina contrato com Pelé para a utilização de seu nome, passando a comercializar uma extensa linha de produtos com essa marca.
O mercado de café, no Brasil, possui cerca de 1200 torrefações, segundo a Associação Brasileira da Indústria de Café, o que não engloba as pequenas torrefações não filiadas e as não regulamentadas. A safra nacional de 2008/2009 – com 51 milhões de sacas - ratifica a posição do Brasil como maior produtor mundial de café. Atualmente, o Brasil participa com 37% da produção mundial de café, seguido pelo Vietnã e a Colômbia com 19 e 10 milhões de sacas respectivamente. A Cacique é uma das maiores indústrias do seu setor em volume de sacas processadas e a segunda de café solúvel, no Brasil. Suas operações estão divididas em três divisões: Solúvel, responsável pela produção de óleo de café, extrato de café e café solúvel (spray dried e freeze dried); Alimentos, responsável pela produção de café torrado em grão, café torrado e moído e cappuccinos; Embalagens, responsável pela produção de sacaria de fios de polipropileno trançado (raffia).
A Divisão Alimentos estabeleceu-se em Barueri/SP em 1979. Em 1997, a fábrica foi totalmente modernizada, trocando todos os equipamentos e incluindo já automação embarcada com CLPs. Essa automação gerava algumas informações que ficavam disponíveis para o operador através da IHM da própria máquina. Porém, essas informações só saíam do chão de fábrica através de relatórios mensais. Esses relatórios eram feitos manualmente. “Quando a informação chegava era só mesmo uma visão contábil porque já não se podia tomar nenhuma providência”, lembra Paulo Rufino de Melo Silva Jr, gerente administrativo financeiro da Divisão Alimentos.
No final de 2004, a unidade começou a utilizar, nas áreas comercial, estoque e finanças, um sistema BI que disponibilizava em tempo real toda a gestão da empresa. “Já tínhamos informações do departamento de contas a pagar, contas a receber, estoque, clientes, logística, etc. Então, precisávamos de um sistema que conseguisse trazer informações on line e em tempo real também do chão de fábrica”. Considerando-se que o mercado de café é extremamente competitivo – o insumo principal tem seu preço ditado pelo mercado (commodity), o preço de venda dos produtos industrializados sofre pressão da concorrência e a centralização dos canais de distribuição - tornava-se vital um controle apurado dos custos e da eficiência industrial. Assim, um dos pontos levantados pela Cacique para ganho de eficiência foi o controle do give away – quantidade de café envasada em cada embalagem que ultrapassa o peso determinado. Se a junção da TI com a automação no chão de fábrica conseguisse reduzir as perdas com o give away, um projeto de aumento de eficiência teria seu custo pago em pouco tempo.
Este tipo de projeto (que considera os interesses de várias áreas da empresa, como produção, contabilidade, comercial e suprimentos) é cercado de dificuldades, até porque os mundos envolvidos são muito distintos. Sem o suporte do pessoal de produção, fica mesmo impossível de ser realizado. Mas na Cacique, o projeto de trazer informações da produção para o corporativo nasceu de uma pergunta bem feita: Como seria possível trazer essa informação da produção, de maneira compreensível, para o corporativo? |
|
Na Divisão Solúvel, a Cacique já trabalhava com um supervisório fornecido pela Softbrasil e, a partir daquela experiência, a Divisão Alimentos imaginou utilizar uma tecnologia similar para suportar esta implementação. Mas desde o primeiro momento ficou claro que a solução necessária não passava pelo uso de supervisórios, mas sim pela implementação de uma ferramenta de MES/MOM (Manufacturing Execution Systems/Manufacturing Operations Management). Para esse projeto, foram avaliadas três empresas e a vencedora foi a Softbrasil, com a solução AMPLA desenvolvida pela Citect. Numa reunião multidisciplinar, com pessoal do laboratório, desenvolvimento, contabilidade, produção e a Softbrasil, foram apresentadas as informações necessárias para o BI. “Falar sobre cubo mágico, wizard, periódicas, métricas e ouvir outros tantos termos novos foi uma fase complexa, mas os recursos disponíveis no Ampla/Citect caíram como uma luva no nosso processo e, por isso, o projeto ganhou o comprometimento de todas as áreas envolvidas” comenta Paulo Rufino.
Um dos desafios mais críticos foi a integração de vários equipamentos de três décadas, que não tinham documentação técnica nem protocolos abertos.
Segundo Rogério Zampronha, da Softbrasil, o trabalho foi um desafio grande porque foi preciso desenvolver drives e interfaces para equipamentos de anos diferentes e de fabricantes distintos; “foi preciso abrir caixas-pretas de automações embarcadas e nem todos os fabricantes de equipamentos colaboraram”.
Entraram no projeto todos os equipamentos envolvidos no processo produtivo, como torradores, moinhos, empacotadoras e check-weighers. Paulo Rufino ressalta que é preciso ter cuidado para elencar os itens que se quer observar. O levantamento realizado depois de um ano de utilização do sistema mostra que o projeto já se pagou com folga porque a empresa já reduziu o give away em 80% e as perdas de embalagem em 50%.
Como o software gera análises por equipamento, linha e/ou produto, a unidade está partindo para análises sobre rendimento, consumo de energia e gás, tempo de batelada, etc. Segundo Paulo, o software possibilita infinitas análises com vários KPIs (Key Performance Indicators, ou Indicadores Chave de Desempenho) para trabalhar inclusive como indicadores junto ao RH.
Colocar o projeto para todas as linhas de uma só vez gerou complexidades na instalação, mas muito mais retorno de informações.
A informação está disponível para quem tem autorização para acessá-la, como de costume. E 2008 foi um ano para colocar o sistema para funcionar, estabilizar, gerar confiabilidade e um histórico de tempo suficiente para não gerar atitudes drásticas e precipitadas. A empresa assinou o contrato de fornecimento em dezembro de 2006 e começou a trabalhar sistemas de ajuste de informação no começo de 2007; a implementação se efetivou em 2008. Levantar informações e requerimentos dos usuários foi a parte mais demorada do projeto e a diferença de cultura pode atrasar um pouco o trabalho. Os consultores entendem muito dos softwares mas necessitam de um tempo maior para se familiarizar com o negócio do cliente e com as necessidades dos usuários. “Esse trabalho faz parte do processo de modernização contínuo de toda a empresa e os responsáveis pelas outras divisões estão acompanhando esse projeto, já se preparando para utilizar esta tecnologia”, conclui Antonio Paulino Martins, diretor da Cacique. “A utilização do Ampla/Citect, pelas outras divisões, será o caminho para uma integração ainda maior da Cacique” finaliza Rogério. |
TAI: a convergência |
Falar sobre convergência entre Tecnologia de Automação e Tecnologia de Informação nos remete à camada MES da pirâmide do setor, a terceira camada, aquela que liga o processo ao corporativo. E, no Brasil, um dos maiores especialistas no assunto é Constantino Seixas Filho, CTO da Accenture Automation and Industrial Solution (AAIS), resultado da incorporação da ATAN pela Accenture, ocorrida em junho deste ano.
Quando se fala em convergência digital cumpre notar que quem lidera esse movimento, estabelecendo as tecnologias, produtos e padrões é a TI, onde a evolução é sempre mais rápida - até porque a TI sempre contou com mais usuários, maiores investimentos. Houve uma forte evolução de hardware e software, padrões de redes, de comunicação e interface com o usuário que a automação passou a adotar, sempre com algum atraso. “Quanto mais em baixo estamos na pirâmide dos sistemas industriais, maior a resistência em relação às novas tecnologias. Há 20 anos, a automação utilizava um conjunto de soluções totalmente particular, a começar do sistema operacional. Quando todo o mundo já usava o Windows 3.1, a automação empregava os chamados Sistemas Operacionais de Tempo Real ou RTOS, como o QNX, AMX, VMS, VXWorks, hoje só usados em aplicações de nicho, quando realmente temos restrições críticas de tempo de resposta. O Windows foi ganhando pouco a pouco espaço nas aplicações industriais. Começou pelos sistemas SCADA e IHMs, lembra Constantino, que credita a rápida aceitação do Windows a partir dos anos 90 à facilidade que as pessoas têm de lidar com paradigmas que já lhe são familiares devido à larga utilização dos computadores no ambiente doméstico e evidentemente ao custo, muitas vezes menor que o de um sistema especial. Mas Constantino ressalta que, quando se pensa no Windows 3.1, tecnicamente ele não satisfazia os requisitos da automação; então houve uma época de convivência entre vários sistemas, os RTOS foram sendo substituídos por uma nova geração de produtos como o OS2 da IBM e o Windows NT da Microsoft. Isto representou uma grande guinada para a automação, tomando rapidamente o espaço do VMS e das várias vertentes do UNIX. “Até mesmo nas universidades, nos cursos de programação concorrente, abrimos mão do RTOS e passamos a adotar o Windows. Foi o reconhecimento de que o Windows havia ganho essa batalha.
O mesmo ocorreu com relação aos aplicativos e o Excel se tornou a ferramenta mais utilizada para a geração de qualquer relatório no ambiente industrial.
“Tem uma piada que diz que o Excel foi a primeira versão de M.E.S. e continua a mais usada até hoje. Se você pergunta a um gerente: você usa algum sistema de gestão da produção?, a resposta é: claro, temos MES: Microsoft Excel Spreadsheet”.
Já do ponto de vista de redes, o padrão vencedor foi o Ethernet, deslocando as redes proprietárias, dedicadas. Dentro da corrente acadêmica todos apostavam nos protocolos do modelo OSI da ISO, mas o stack que ficou na prática foi o TCP/IP. Criado para viabilizar a Internet, o TCP/IP se estabeleceu primeiro na área de TI e agora é utilizado também na automação. É importante salientar que a própria Internet foi um paradigma vencedor. Hoje todos querem acessar dados do ambiente industrial via web. Você pode estar em Nova York e mostrar os dados de produção de sua fábrica em São Paulo em tempo real.
Alguns protocolos da suíte TCP/IP como o SNMP – Simple Network Management Protocol, atenderam primeiro o gerenciamento de dispositivos gerenciáveis de TI (switches, roteadores, servidores, etc) oferecendo reports de erros, detecção de bottlenecks e centenas de parâmetros de desempenho da rede. Depois, o padrão passou a ser importante também para a automação, porque com ele é possível se ter o diagnóstico de centenas de equipamentos. É um protocolo antigo, que está tendo uma releitura moderna devido ao boom do gerenciamento de ativos. Hoje se faz diagnóstico de equipamentos de TI e TA com SNMP. O HTTP (Hypertext Transfer Protocol), um dos mais antigos protocolos desta suíte é hoje a base dos web services, a maneira mais moderna de se interligar aplicativos, sejam eles de automação ou de TI. Desta froma a suíte TCP/IP de protocolos se torna evidência de mais um ponto de convergência.
Constantino lembra que o próprio OPC – Ole for Process Control é um fenômeno desse movimento: a Microsoft (que desenvolveu a tecnologia OLE Object Linking and Embedding hoje denominada COM – Component Object Model) falava de um padrão para chão de fábrica e a maioria dos especialistas de automação achou que não ia pegar. Mas o OPC se tornou um sucesso avassalador. O OPC simplificou muito o trabalho para a automação, porque o fornecedor de um equipamento agora fornece apenas um servidor OPC e o fornecedor do SW que consome os dados, o SCADA, por exemplo, só tem que desenvolver um cliente OPC e os sistemas se conectam. Antes, do ponto de vista da automação, era preciso que especialistas desenvolvessem drives especiais para cada combinação de sistema SCADA, sistema operacional, placa de comunicação e CLP ou outro dispositivo de campo. “Precisávamos de profissionais muito capacitados e caros que gastavam de dois a três meses para desenvolver um produto extremamente sofisticado e que raramente podia ser reutilizado. Implicava em muito investimento e pouco retorno.”
O sucesso da adoção de padrões de TI na automação aconteceu porque houve uma simplificação e barateamento dos sistemas, espalhando a automação dos segmentos mais intensivos em capital para indústrias, onde esse custos antes eram proibitivos. Houve uma democratização da automação.
Imagine uma sala de controle antiga com as suas mesas de controle em aço, seus painéis sinóticos de dezenas de metros na parede, tudo ocupando centenas de metros quadrados de área. O PC substituiu tudo isso. Passou-se a fazer tudo no computador e a operar a planta com o uso de um mouse. Tudo a um custo uma dezena de vezes inferior.
Todos querem operar um sistema amigável, usando janelas, transferindo informações facilmente de um diapositivo para outro, publicando informações na web, visualizando informações convenientemente formatadas nos portais dos centros de inteligência operacional e isso foi o que nos trouxe a convergência digital. Deixamos as especiarias para quem constrói foguetes e aviões.
Outra revolução se deu no tratamento das informações. As equipes não sabiam o que fazer com os muitos dados vindos dos CLPs e sistemas Scada, além de formatar relatórios para engenheiros e operadores de processo. “Era preciso produzir informação e não se sabia direito nem o que era informação! A maioria acha que produzir informação é coletar dados para a engenharia, num conceito bottom up. Mas a informação é na verdade uma resposta a uma pergunta formulada”, ressalta Constantino. A pergunta vem antes! Então é preciso perguntar para o usuário o que ele usa, o que ele precisa saber para realizar suas funções. O conceito é top-down. Entre o ERP e a automação foi introduzida uma série de sistemas formando o que hoje chamamos de terceira camada. Surgiram o PIMS- Plant Information Management System, o MES – Manufacturing Execution System, o LIMS, Lab Information Management System e o PAM – Plant Asset Management. A esses sistemas que gerenciam todas as informações da produção, da manutenção da qualidade e dos estoques (inventário) agregamos uma camada de operations analytics, isto é, ferramentas de tomada de decisão. Essa última ferramenta é chamada de EMI – Enterprise Manufacturing Intelligence e é onde damos mais um passo no processo de converter informação em conhecimento e finalmente em ação.
A entrada radical da TI no ambiente industrial teve um impacto muito grande e trouxe muitas distorções. A primeira pergunta é: quem vai ser o dono dessa nova camada? Quem irá definir e ser responsável pelos sistemas de nível 3 ? Tanto TI como automação querem ser os protagonistas dessa nova atividade de gestão da produção, mas devido a ser uma área de sobreposição de competências criamos um novo nome para designar essa atividade. Nós a chamamos de TI industrial (Industrial IT) e deixamos claro que essa atividade requer um novo tipo de profissional que não existia há alguns anos atrás. |
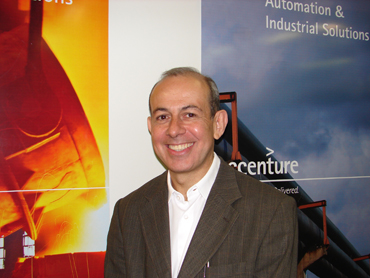 |
Constantino: indústria quer colher resultados rápidos |
|
Foi quando algumas universidades criaram um novo curso de engenharia denominado Engenharia de Controle e Automação para formar essa nova geração de profissionais que entendem tanto de controle como de tecnologia da informação. A UFSC foi a pioneira, seguida logo depois pela PUC Minas e UFMG. Como professor da UFMG, Constantino vem acompanhando a evolução da mão de obra do setor e lembra que o curso de Engenharia de Automação tem feito muito sucesso e tem captado uma boa fatia de bons alunos nos vestibulares, porque a profissão se mostra mais atrativa a cada dia. Era difícil convencer um jovem a se dedicar à instrumentação convencional, mas todos querem trabalhar com gerenciamento de ativos, que acessa a mesma instrumentação através de sistemas de informação modernos.
Por outro lado os antigos profissionais de automação e de TI tiveram de ser reciclados e a ISA está tendo um papel importante nesta história. Estamos ministrando cursos de PIMS, MES, padrão de comunicação OPC, etc. Para se adaptar aos novos tempos a ISA acaba de mudar de nome. Ela deixa de ser a Instrument Society of América para se tornar International Society of Automation. Ela mesma se coloca agora como uma entidade que trabalha não só com automação, mas também com sistemas.” A ISA passou a desenvolver padrões como o ISA 95, norma que mostra como comunicar automação com sistemas de negócios; o ISA 99 que trata de cyber security no ambiente industrial; o SP 100, que estabelece padrões para comunicação wireles em ambiente industrial.
Os antigos profissionais de TI e automação devem encarar toda essa mudança como uma oportunidade e não como uma ameaça. Afinal são centenas de novas atividades que estão sendo criadas e todos nós podemos participar dessa evolução. A Accenture acaba de criar um curso chamado “Automação para executivos” visando passar conceitos de automação e de sua importância para os negócios, para profissionais de TI e outras áreas que após um processo de definição de governança passaram a assumir atividades de automação.
Hoje, as pessoas têm menos preconceito porque é inexorável essa penetração da TI na automação, é mais fácil e mais barato, vai habilitar a automação para um número maior de usuários. Mas esse acoplamento de TA e TI precisa ser bem feito para que não haja problemas de governança. Isso porque em geral existe nas indústrias um departamento de TI muito bem sedimentado, ligado a uma diretoria corporativa, uma área bem estruturada com profissionais caros e bem preparados. Já a automação, via de regra, ou não existe como entidade, ou está mal colocada no organograma da empresa. É comum constatar que a automação nasce debaixo área de manutenção, com duas ou três pessoas encarregadas da atividade de conceber, implantar e manter sistemas, mas sem orçamento nem força para atingir seus objetivos.
Uma das grandes preocupações hoje é estabelecer uma boa governança entre TA e TI, ou seja, redefinir a colocação das duas áreas para que atuem de forma sinérgica e para que tenham conhecimento e poder suficientes para implantar projetos conjuntos. Essa boa governança é fundamental quando se faz, por exemplo, o Plano Diretor de Automação e Informação que pode gerar um port-folio de projetos a serem implantados. Sem estrutura adequada, tanto a implantação dos projetos como a sua sustentabilidade se torna impossível. Em algumas empresas essas áreas ficam duelando ou estabelecem fronteiras arbitrárias, nocivas para a organização. Os prejuízos advindos de uma má gestão entre TA e TI são incalculáveis. “ Num estudo de governança todos os processos de TA e TI são mapeados e as responsabilidades definidas” , explica Constantino.
O relacionamento e os limites de atuação devem ser definidos caso a caso. Existe uma orientação geral, a ISA 95, que ajuda a estabelecer essas fronteiras, e a trabalhar a convergência. A norma é forte na divisão de funcionalidades entre ERP(TI corporativo) e MES (TI Industrial) e se preocupa muito com o papel dessas duas camadas dentro da organização.
Dependendo do porte da organização existe a automação estruturada em paralelo ou subordinada à área de TI. Automação e engenharia de processo possuem também grande afinidade e essa terceira área pode vir a formar um tripé com TA e TI em muitos tipos de indústria. É interessante como a Accenture reconheceu esse movimento, entendeu que TA e TI têm que andar juntas e adquiriu a ATAN, empresa brasileira com tradição em automação e TI Industrial , tornando-se a primeira empresa capaz de fornecer uma solução do nível corporativo à instrumentação.
É preciso corrigir muitas distorções de mercado. Em projetos greenfield, por exemplo, é normal incluir toda automação dentro do escopo de uma EPCista que realiza todas as definições de projeto. Geralmente isso é feito sem se ter conhecimento de como as camadas Automação, MES e ERP irão atuar. Uma EPCista sabe tratar muito bem mecânica, civil, elétrica, tubulação e muitas vezes instrumentação, mas não tem vocação de automação e de TI e acaba gerando um projeto com distorções difíceis de serem resolvidas a posteriori. Esse espaço será rapidamente alterado para acomodar as empresas que têm essa visão integrada de TA + TI .
No caso do nível 3 existe uma série de ferramentas: o PIMS, o MES, o LIMS – Lab Information Management System, e,o Asset Management, entre outros sistemas. O álbum de figurinhas da automação se ampliou e permite diagnósticos cada vez mais precisos de qualquer tipo de anormalidade seja na infra-estrutra, nos equipamentos ou no processo. Toda essa informação sobe para o centro de inteligência operacional (CIO), remote operating center(ROC), remote intelligence center (RIC) ou qualquer outro nome que se queira dar . Na sala de inteligência a informação vai estar disponível para o operador e para o engenheiro responsável entender o que está acontecendo no processo e a partir daí formular as práticas líderes – que partem da medição e visualização do que acontece na fábrica para tornar possíveis comparações com padrões do mesmo grupo e/ou de empresas do mesmo segmento de mercado. Pode-se fazer benchmarking entre unidades da mesma companhia, entre diferentes linhas de produção, e mesmo entre equipes. A simples comparação de paradas entre linhas, por exemplo, já permite visualizar e equacionar uma série de problemas que aumentam a disponibilidade dos ativos de produção.
As ferramentas de “TAI” são muitas e valiosas, mas, numa época como agora, em que é preciso fazer muito mais com muito menos, essas ferramentas precisam trazer ganhos extremamente rápidos principalmente com a mudança de foco das indústrias. Há alguns meses, o objetivo era o aumento de produção e, agora buscamos a redução de custo, extrair o máximo dos ativos e aumentar o rendimento.
E Constantino avisa: “ Temos que trabalhar indicadores-chave simples de medir e trazer retorno rápido. O OEE – Overall Equipment Effectiveness, o consumo específico de energia e de reagentes são alguns desses indicadores. Hoje o investimento com retorno em um ano não atende; estamos fazendo planos curtos, fazendo intervenções agora para colher resultados em quatro meses. As ações de curto prazo são muito importantes num cenário econômico desfavorável, mas não se esqueçam das mudanças estruturais. Só elas irão permitir o crescimento em bases sustentáveis. E isso só se alcança com TAI e boa governança”. |
|
LEIA MAIS
NA EDIÇÃO IMPRESSA |
|
DESEJANDO
MAIS INFORMAÇÕES: redacao@editoravalete.com.br
|
|
Leia mais na edição impressa |
Retrospective |
Brazil Automation |
ISA Show debate a crise e traça panorama positivo para o mercado de automação |
Profile Altus: pioneirismo e experiência |
Special |
Inovações em nanotecnologia prometem revolucionar a economia |
Abinee alerta dependentes de insumos importados |
Flash |
Certificação é alvo de críticas durante CIAEx 2008 |
Convergência entre chão-de-fábrica e corporativo dá tonalidade da Automation Fair |
|